The Most Advanced Ball Mill Design Free Consultation
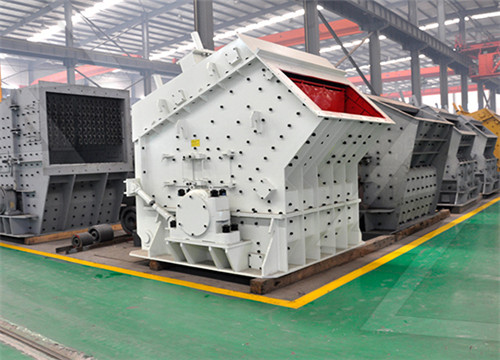
A Review of Advanced Ball Mill Modelling J-STAGE
A Review of Advanced Ball Mill Modelling. in particular ball mills, analyzing critically various approaches proposed, their limitations and achievements, identifying areas that
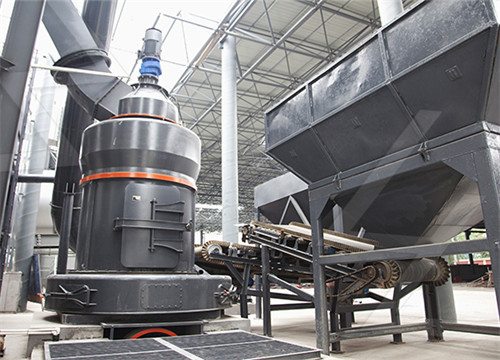
Ball Mill Application and Design Paul O. Abbe
Ball Mill Application and Design. Ball mills are used the size reducing or milling of hard materials such as minerals, glass, advanced ceramics, metal oxides, solar cell and
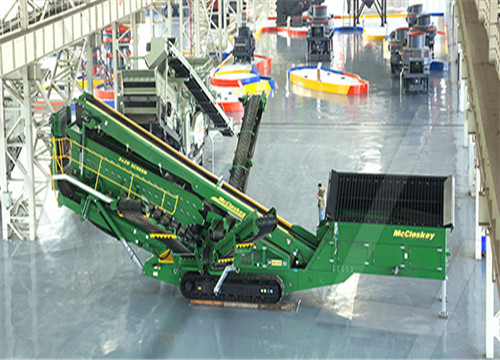
Ball Mill Design/Power Calculation Mineral Processing
2015年6月19日The basic parameters used in ball mill design (power calculations), rod mill or any tumbling mill sizing are; material to be ground, characteristics, Bond Work
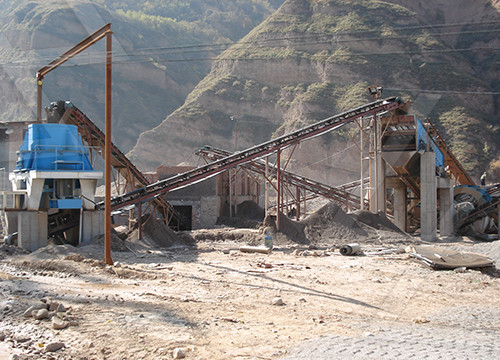
(PDF) Design of Three-chamber Ball Mill ResearchGate
2021年1月1日In this , the design method of three chamber ball mill is introduced. Comchambered with the design of Φ 3.5 × 13m three-chamber ball mill, the design
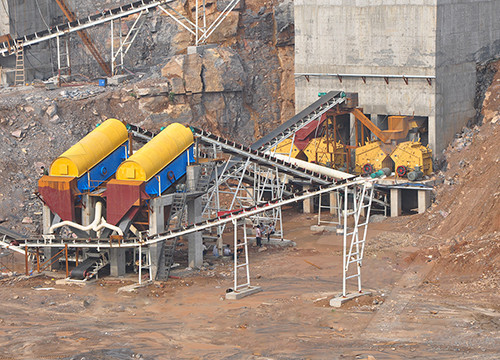
Ball Mills Industry Grinder for Mineral Processing JXSC
Ball mill, also known as ball grinding machine, is a well-known ore grinding machine, is widely used in mining, construction, aggregate application. JXSC start the ball mill
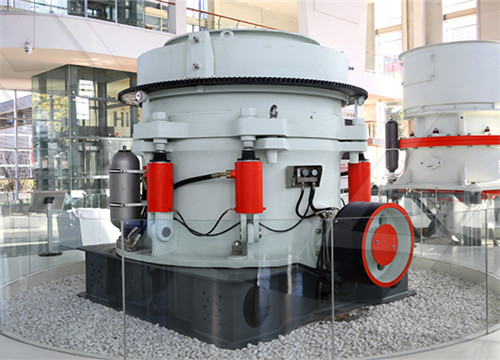
(PDF) A Review of Advanced Ball Mill Modelling
2017年1月15日View. Show abstract. The most advanced approach to simulate ball mills emerged in the early 1990s, by combining information from the mechanical
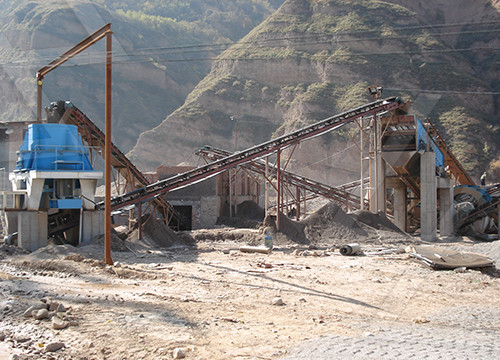
Ball Mill Liners Selection and Design Ball Mill Rubber Liner
2020年5月19日The ball mill liners are located on the inner surface of the ball mill barrel, which protects the barrel from the direct impact and friction of the grinding media and the
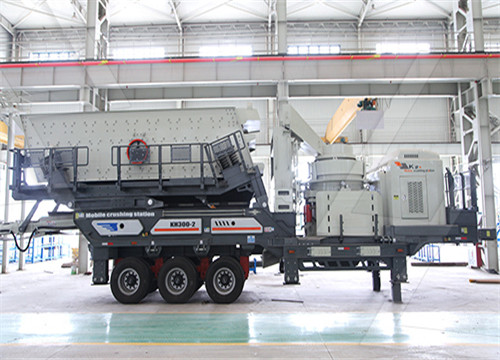
How to design a Ball Mill GrindingClassification Circuits
You also need a rod mill work index to design a ball mill operating on a coarse feed, above about 4 mm. Q1: You design for a typical percentage of critical speed, usually 75% of
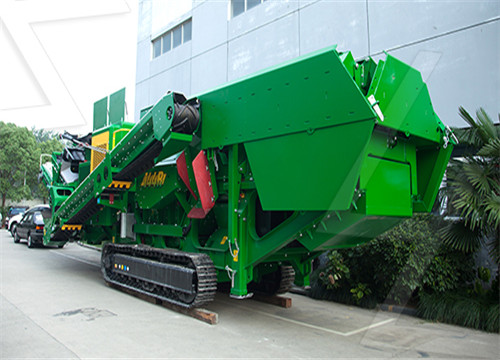
An integrated system development for ball end mill
2005年1月26日The purpose of this stone is to provide a reasonable means to approach tool shape optimization of ball end mill for high-speed milling operation. The stone
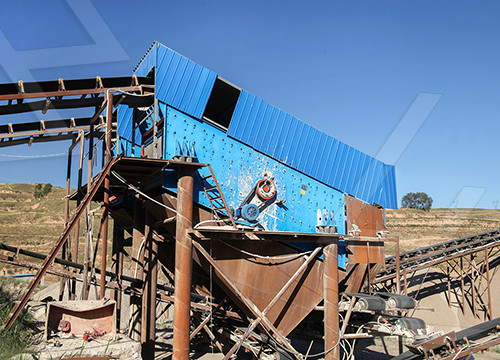
A Review of Advanced Ball Mill Modelling
The mill dimensions, 30 cm in diameter and 30 cm in length, and the test conditions are standardized, with a maximum ball size of 40 mm and an ore top size of 3.35 mm. With less than 300 balls, it poses no challenge in running the simulations, if only grinding media are included (Fig. 1).
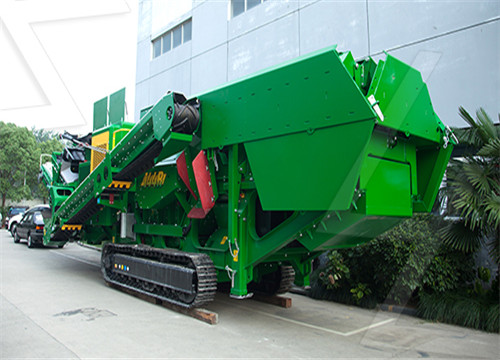
Ball Mill Application and Design Paul O. Abbe
Click to request a ball mill quote online or call 630-350-3012 to speak with an expert at Paul O. Abbe® to help you determine which design and size ball mill would be best for your process. See our Size Reduction Options Steel Ball Mills Benefits of Tumble Milling: 1.
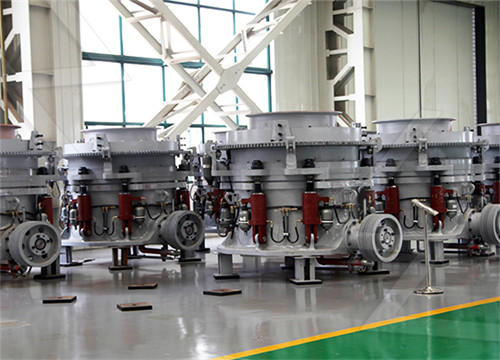
(PDF) Design of Three-chamber Ball Mill ResearchGate
2021年1月1日Ball mill is a kind of raw material processing machinery which plays the role of grinding. Its working principle is that the movement and force are transmitted to the barrel of ball mill...
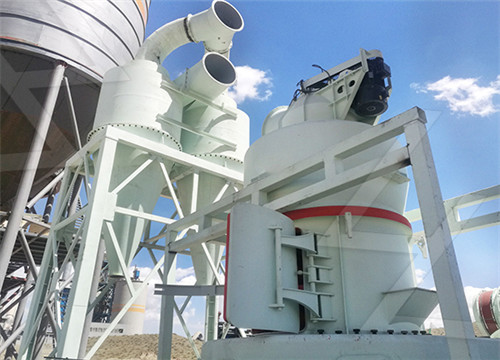
Grinding Mill DesignBall Mill Manufacturer
2017年2月20日The grinding charge in a ball mill consist of cast or forged steel balls. These balls are fed together with the feed and consequently ball mills can be in operation for months without stopping. The ball size is

An integrated system development for ball end mill design,
2005年1月26日The purpose of this stone is to provide a reasonable means to approach tool shape optimization of ball end mill for high-speed milling operation. The stone presents a new development of an integrated system for ball end mill design, creation and evaluation that is more flexible and more systematic than the commercially available tool
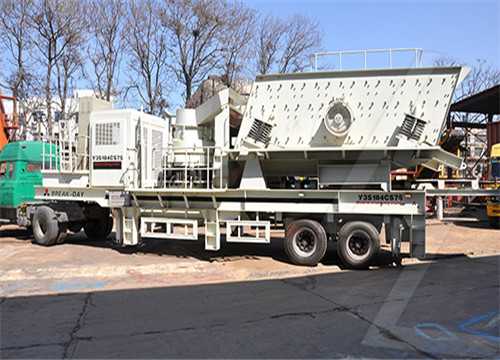
(PDF) A Review of Advanced Ball Mill Modelling
2017年1月15日The most advanced approach to simulate ball mills emerged in the early 1990s, by combining information from the mechanical environment in ball mills, obtained using the discrete element...
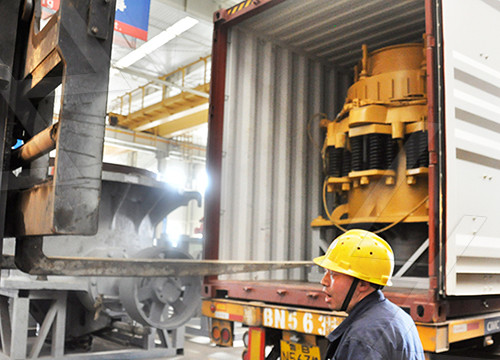
Design Method of Ball Mill by Discrete Element Method
1. Effects of Fins on Ball Motion in the Mill To predict ball mill grinding behavior using the dis-crete element method, we must first be able to repro-duce the balls’ motion in the ball mill using simula-tions. Kano et al.8) have made it clear that it is possible to reproduce the ball motion when the solid material is
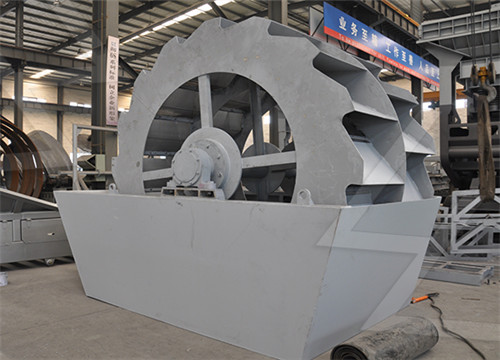
How to design a Ball Mill GrindingClassification Circuits
You also need a rod mill work index to design a ball mill operating on a coarse feed, above about 4 mm. Q1: You design for a typical percentage of critical speed, usually 75% of critical. Then you iterate the mill diameter using a Morrell C-model or equation to get the RPM that corresponds to 75% for that mill diameter.
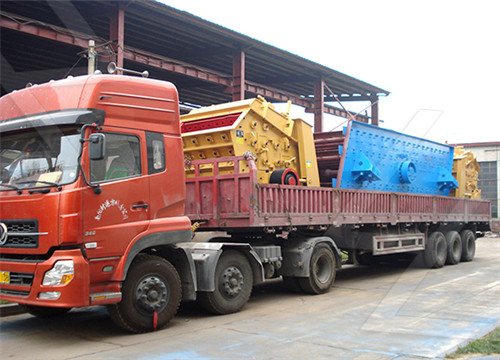
Ball Mill Liners Selection and Design Ball Mill
2020年5月19日The ball mill liners are located on the inner surface of the ball mill barrel, which protects the barrel from the direct impact and friction of the grinding media and the material. The ball mill liners’ material and
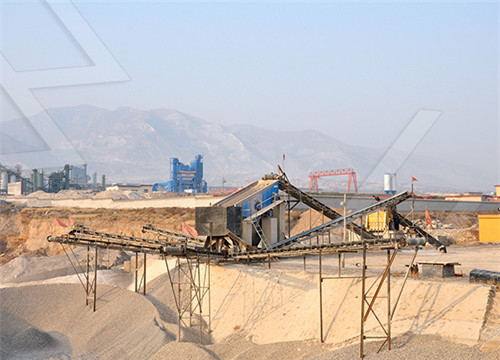
Ball Mills PSP Eng
Ball mills Ball mills are used for dry and wet grinding of different materials such as cement materials, cement, lime, and ceramic materials. PSP Engineering has continuously refi ned the design of its ball mills. Horizontal ball mills have become a reliable part of grinding plants Main characteristics of ball mills seated on shoe-type bearings
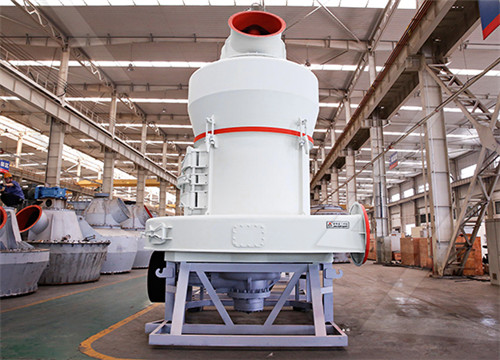
DRUM MILL TM 500 RETSCH
The Drum Mill TM 500 is a laboratory ball mill designed to grind large sample volumes up to 35 l. It accepts initial feed sizes of up to 20 mm and can achieve grind sizes down to 15 µm by friction and impact. Hard, brittle or fibrous samples are pulverized in the 150 l drum filled with 80 kg grinding balls. The variable speed of 10 to 50 rpm
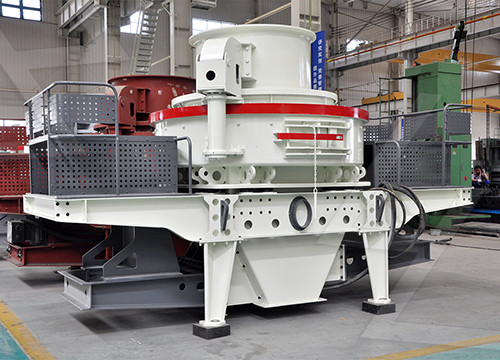
Ball Mills Manufacturers, Suppliers, Exporters TradeKey
Tradekey offers high energy ball mills designed with advanced material development techniques to execute all types of nano degree grinding operations. Any sort of grinding media whether coal, pigments, and felspa can be grinded into finest particles with our technically advanced ball mills.
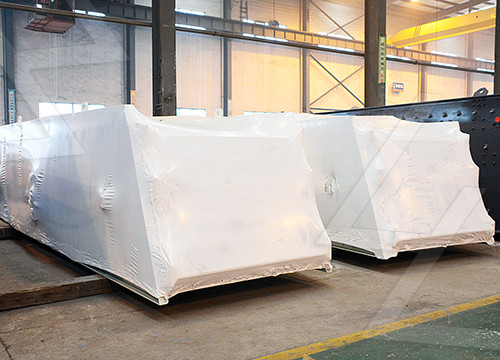
Top 5 product-specific milling technologies used in industrial
2017年7月7日The most common pin mill design is the single rotating pin disc design with stationary door disc and narrow grinding chamber. Centrifugal forces generated by the rotating disc causes the material to radially pass through a labyrinth of pins aligned in circular rows. Material is reduced in size by impact as it passes through the rows of pins.
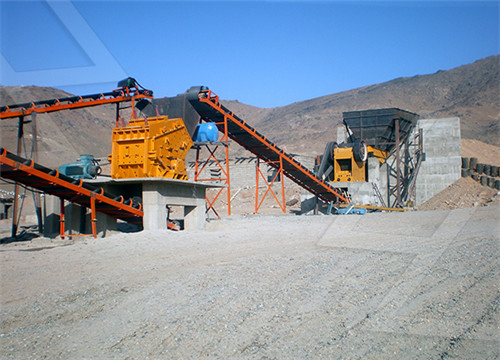
Experimental investigations and modelling of the ball motion in
2011年9月15日A laboratory scale planetary ball mill ( Retsch PM400) was equipped with a test rig which enables the observation and recording of the grinding ball motion inside the grinding chamber. A high speed camera was fixed on the sun wheel (Fig. 1). Lighting is supplied by several LEDs and spotlights, respectively.
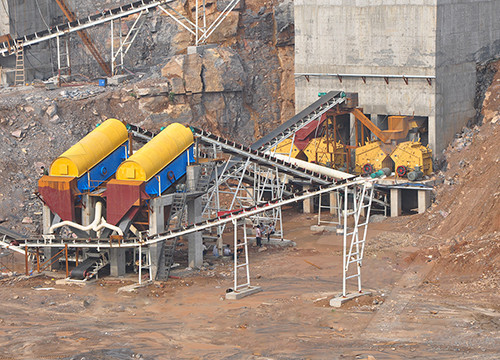
DRUM MILL TM 500 RETSCH
The Drum Mill TM 500 is a laboratory ball mill designed to grind large sample volumes up to 35 l. It accepts initial feed sizes of up to 20 mm and can achieve grind sizes down to 15 µm by friction and impact. Hard, brittle or fibrous samples are pulverized in the 150 l drum filled with 80 kg grinding balls. The variable speed of 10 to 50 rpm
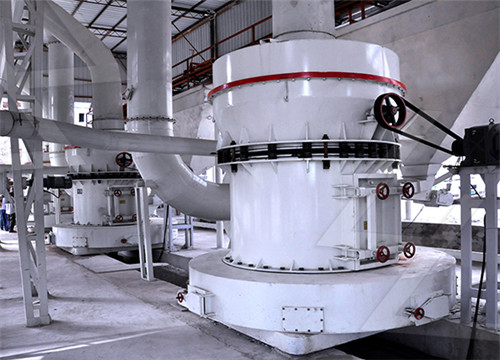
A Review of Advanced Ball Mill Modelling J-STAGE
stirred media mills and high-pressure grinding rolls, ball mills still retain a significant part of their importance in grinding, being widely used from minerals and cement, to chemicals and ceramics. The operation of a ball mill is a capital- and energy-intensive process, so that even mar-ginal improvements in their efficiency result in immense
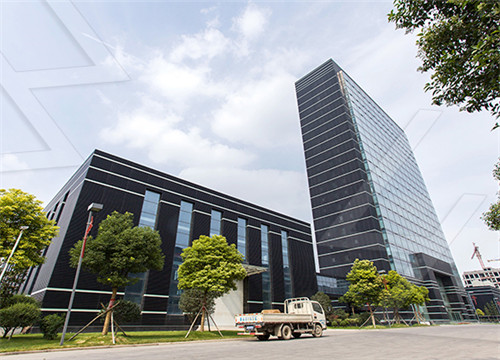
An integrated system development for ball end mill design,
2005年1月26日The purpose of this stone is to provide a reasonable means to approach tool shape optimization of ball end mill for high-speed milling operation. The stone presents a new development of an integrated system for ball end mill design, creation and evaluation that is more flexible and more systematic than the commercially available tool
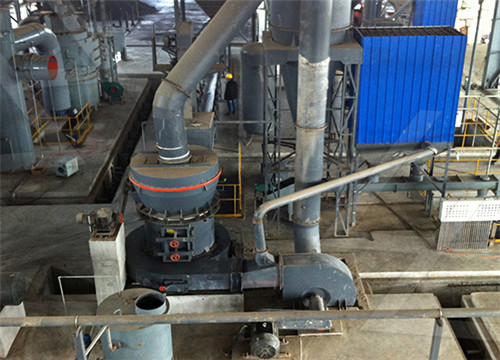
Optimization Of Ball Mill Feeding Device Design ball mills
the ball mill. In order to increase the feed rate of the ball mill and further increase the production capacity, technical experts have made the latest improvements to the ball mill design calculation. affects Problems Existingnumberin the Ball Mill Design of Feed Inlet The hourly output of the ball mill is greatly affected by the feed rate.
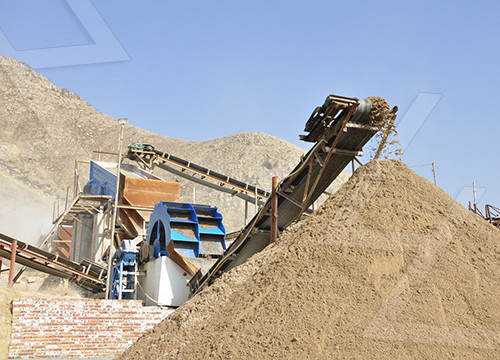
Grinding Mill DesignBall Mill Manufacturer
2017年2月20日The grinding charge in a ball mill consist of cast or forged steel balls. These balls are fed together with the feed and consequently ball mills can be in operation for months without stopping. The ball size is
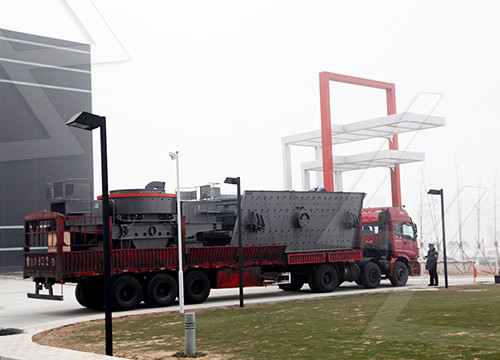
Ball Milling The Role of Media and Bead Mills BYK
Basket bead milling is a relatively new design for ball milling applications. The grinding media is contained in a cylinder (basket), and the mill base is circulated through the basket. The VMA-Getzmann basket mill consists of a stainless-steel cylinder with an opening at the top and a sieve filter on the bottom. The mill base and grinding
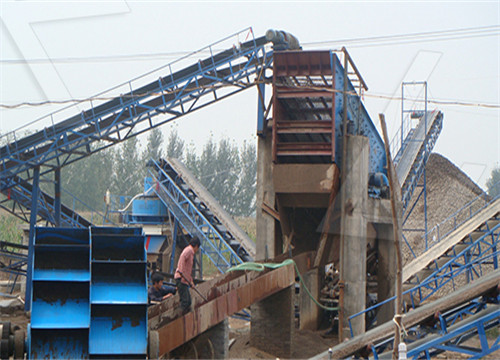
Ball Mills PSP Eng
Ball mills Ball mills are used for dry and wet grinding of different materials such as cement materials, cement, lime, and ceramic materials. PSP Engineering has continuously refi ned the design of its ball mills. Horizontal ball mills have become a reliable part of grinding plants Main characteristics of ball mills seated on shoe-type bearings
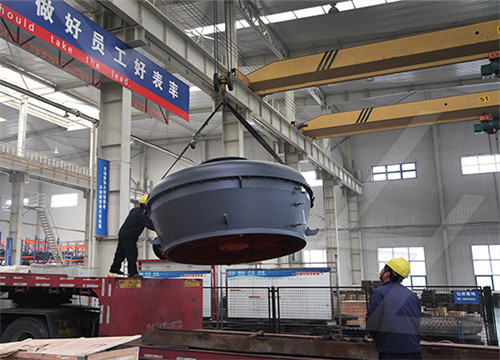
Design Method of Ball Mill by Discrete Element Method
1. Effects of Fins on Ball Motion in the Mill To predict ball mill grinding behavior using the dis-crete element method, we must first be able to repro-duce the balls’ motion in the ball mill using simula-tions. Kano et al.8) have made it clear that it is possible to reproduce the ball motion when the solid material is
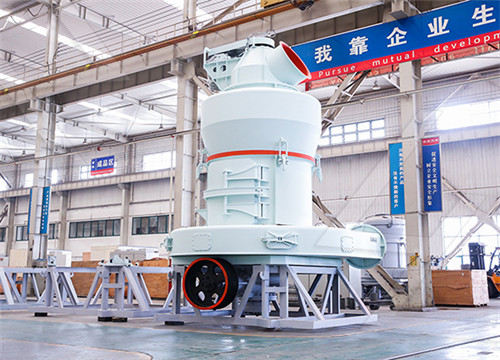
(PDF) A Review of Advanced Ball Mill Modelling
2017年1月15日The most advanced approach to simulate ball mills emerged in the early 1990s, by combining information from the mechanical environment in ball mills, obtained using the discrete element...
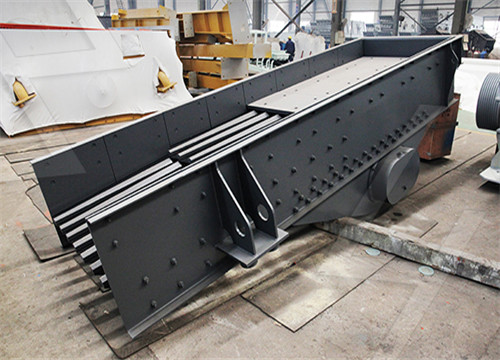
How to design a Ball Mill GrindingClassification Circuits
You also need a rod mill work index to design a ball mill operating on a coarse feed, above about 4 mm. Q1: You design for a typical percentage of critical speed, usually 75% of critical. Then you iterate the mill diameter using a Morrell C-model or equation to get the RPM that corresponds to 75% for that mill diameter.
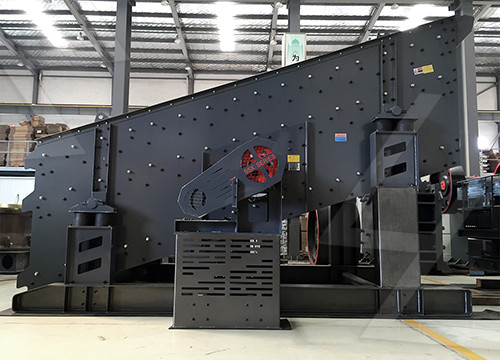
Copper Ball Mill
The copper ore ball mill newly designed by the AGICO GROUP technical team fully incorporates the German advanced ball mill design concept, which mainly includes the structure of the barrel, steel balls, bearings,
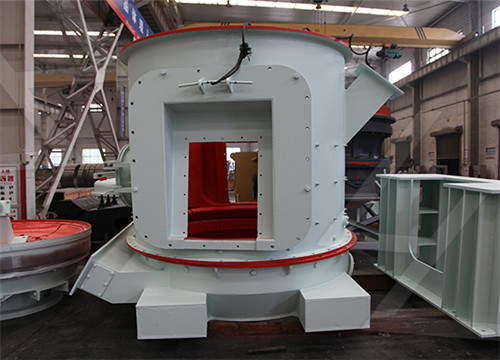
Ball Mills Manufacturers, Suppliers, Exporters TradeKey
Tradekey offers high energy ball mills designed with advanced material development techniques to execute all types of nano degree grinding operations. Any sort of grinding media whether coal, pigments, and felspa can be grinded into finest particles with our technically advanced ball mills.
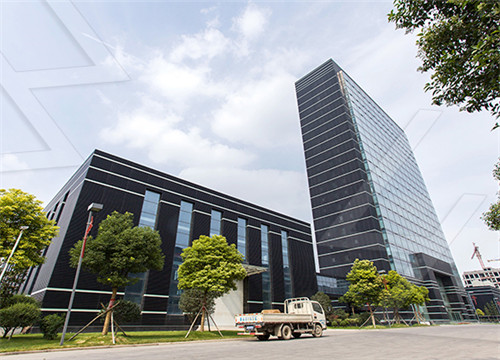
Cement Clinker Ball Mill Manufacturer from Yamuna Nagar
Rs 60 Lakh / Piece Get Best Price. We bring forth a highly advanced Ball Mill, specifically engineered for both wet as well as dry cement grinding applications. Classified depending on the circuit design, bearing, grinding type and drive, the selection is made on the basis of the product fineness, quality, and nature of raw material, site