Abstract Fls Raw Mill Blending Silos: Advanced Technology For Ne
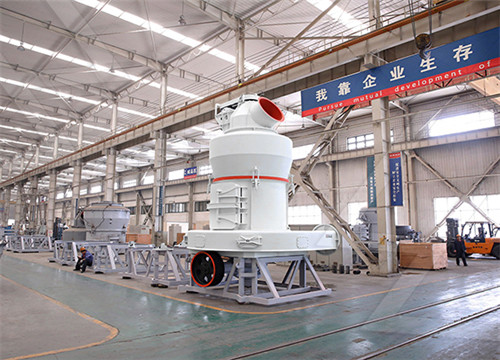
Silos, storage and reclaim solutions
根据热度为您推荐•反馈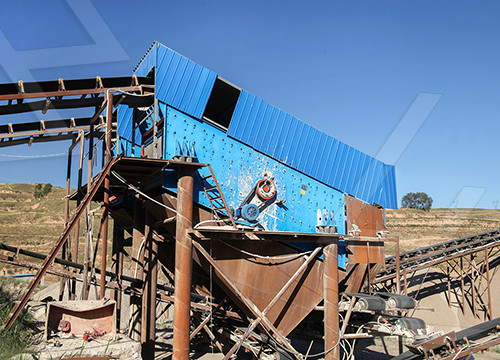
Blending Silos: Advanced Technology for New and Existing
根据热度为您推荐•反馈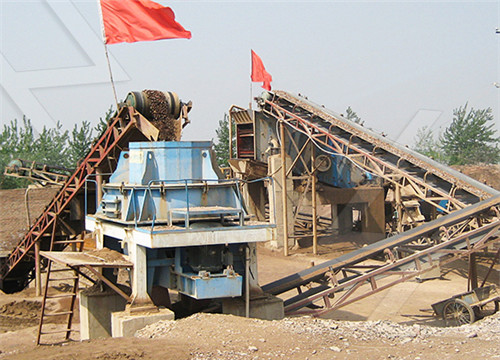
CFI silo
has developed the CFI silo for storage of cement and related products based on the experience gained with the CF (Controlled Flow) raw meal blending and storage
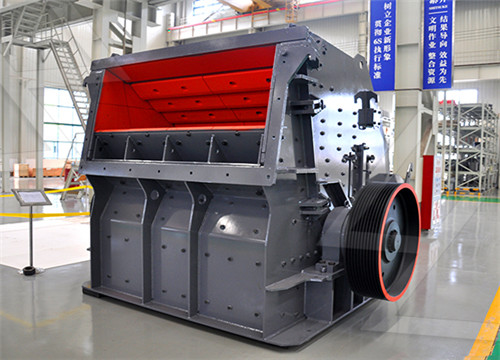
Superior chemical control for the cement industry
Tight control of raw material blending negates the requirement for expensive blending silos. Silos can be considered storage buffers only and this dramatically reduces the
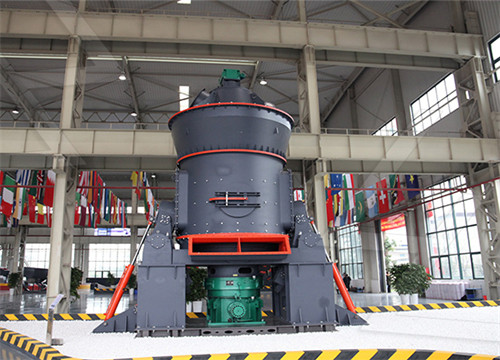
Birla Shakti
Control measures by installing Bag House for Raw mill/Kiln, ESPs for Grate Cooler; Bag filter for cement mill, lime stone crushing, Blending silo, Cement silo, Clinker stockpile,
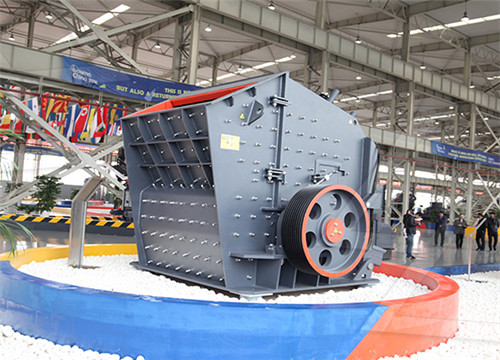
sbm/sbm raw mill blending silo.md at master sbm Codeberg
You can not select more than 25 topics Topics must start with a letter or number, can include dashes ('-') and can be up to 35 characters long.
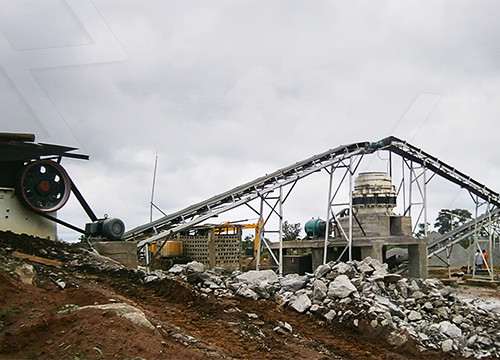
abstract fls raw mill iisslucapaciolo.it
Fls Ball Mill Horizontal 13 6 4 2 . mill self disengagement barring systems fls ball mill horizontal 13 6 4 2 content 1 abstract 2 introduction 3 background 4 mill detail 5
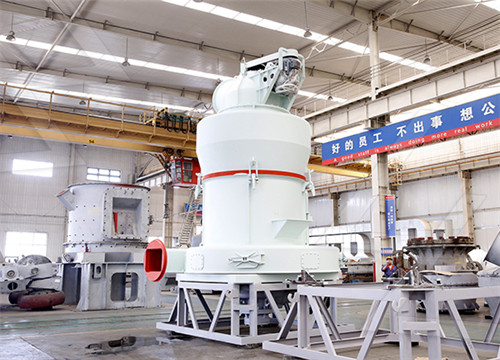
abstract fls raw mill razoriteolivedale.co.za
Abstract Fls Raw Mill Blending Silos Advanced Technology For Ne. SPIRAL SILO Brief Spiral folded silo technology is originated from Germany and SRON modify their
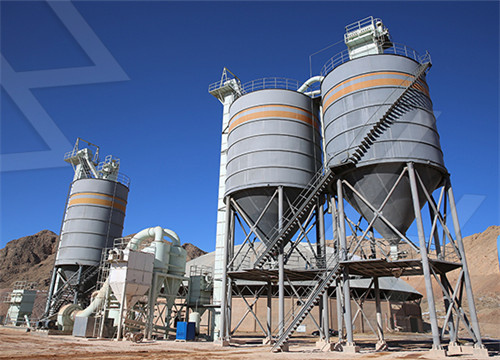
sbm/sbm process raw mill to silo.md at main
Contribute to chengxinjia/sbm development by creating an account on GitHub.
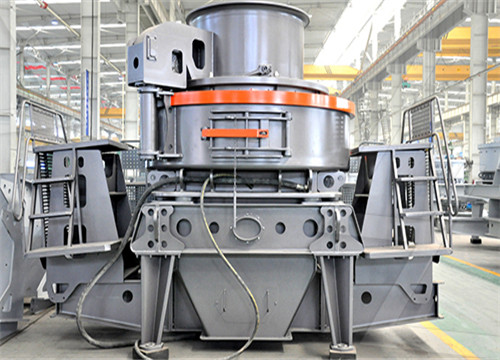
Emission reduction through process integration and exploration of
2023年1月7日The product, after grinding from the raw mill, is transported via air slides and bucket elevators to the homogenizing silo. Homogenizing silo is the prerequisite for raw mill blending to achieve kiln feed consistency. This also ensures regulated feed with minimum variation in quality for the smooth operation of the kiln. The raw mill is
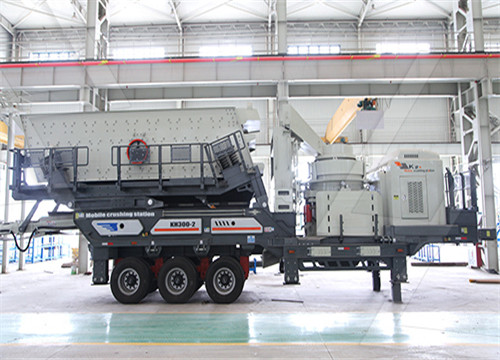
Pneumatic conveying systems Moving dry bulk materials
We are a world leader in the design and supply of pneumatic systems for dry bulk materials. Our products and systems hold longstanding patents on several well-known technologies, and provide clean, safe and cost effective solutions for many diverse applications. Services Pneumatic conveying services Stay updated on your industry
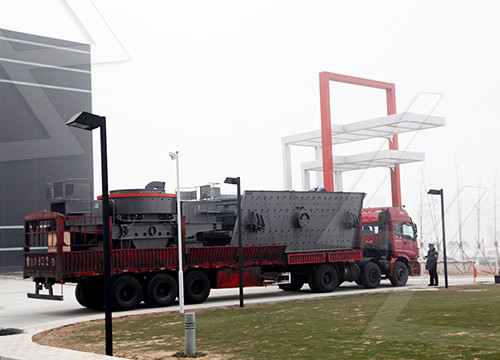
Blending systems and control technologies for cement raw
Diminishing the size and complexity of blending and stocking equipment before and after the raw mill represents a common strategy for reduction of capital and operating cost. The stone discusses the choice between X-ray fluorescence (XRF) and /spl gamma/-ray analysis sensors. Cross belt analysers used in the stockyard are also discussed.
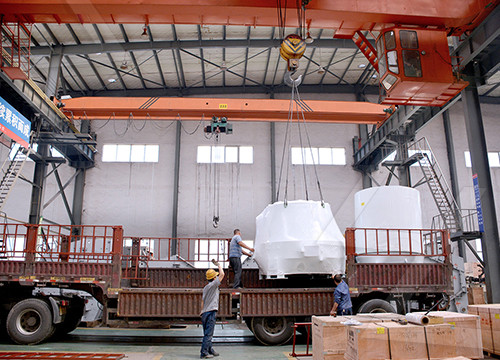
CFMI silo
raw meal blending and storage silo and with the CFS (Controlled Flow Storage) storage silo. The key word in the design of the CFMI silo is reliability. The challenge Ceiling of 4-compartment silo Bottom of 2-compartment silo. Project Centre Denmark A/S Vigerslev Allé 77 DK-2500 Valby Copenhagen Tel: +45 3618 1000 Fax: +45 3630 1820
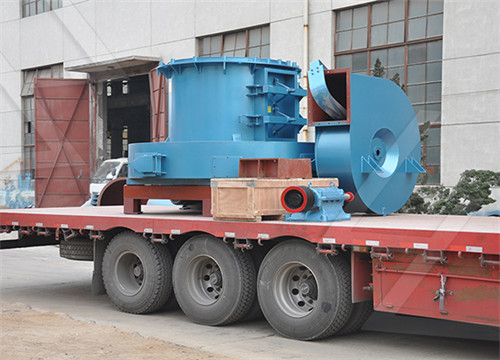
Silo Technology Zeppelin
Zeppelin Multi-Flow blending silo Applications The versatile blender is suited for bulk materials with easy to poor flowability and is suitable both for continuous and discontinuous blending. The Multi-Flow blending silo is the ideal choice partic-ularly for retrofitting conventional silos with blending technology. System description
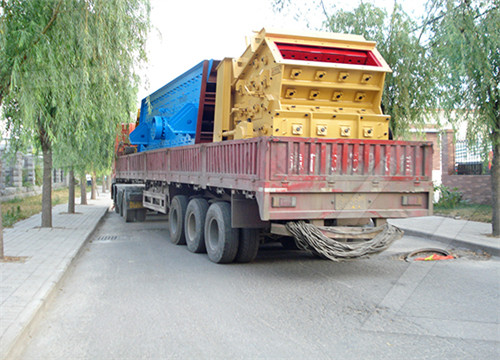
Azerbaijani cement production by Norm Sement Global Cement
2015年12月8日The raw meal is collected from the bag house filter hoppers and transported to a 550t/hr bucket elevator that feeds into an inverted cone-type blending silo with a design-blending ratio of 7:1. The 20,000t capacity blending silo can supply enough raw materials for 2.5 days of kiln operations. Under the blending silo there is a 180m 3
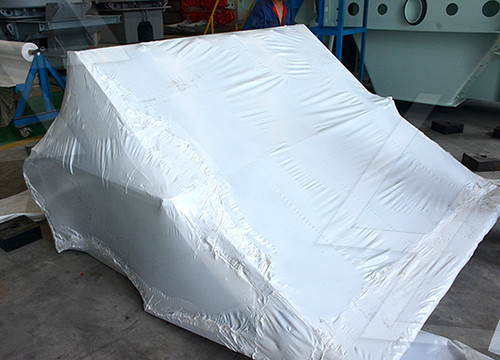
Birla Shakti
An electrostatic precipitator/bag house de-dusts the raw mill gases and collects the raw meal for a series of further stages of blending. The homogenized raw meal thus extracted is pumped to the top of a preheater by bucket elevator. In Pre-heaters the material is
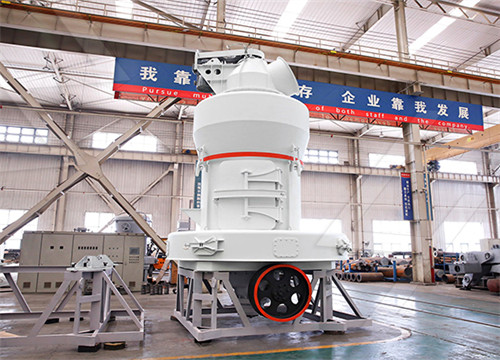
Raw Material for Cement Cement Blending |Amrit Cement
90 95% of Limestone, 2 5% of Clay and 3 5% Laterite. The above mix proportion is ground in Raw mill at 110 118TPH (Ball mill) to achieve desired fineness and fed into CF silo (continuous Flow silo concreted, capacity 4500MTs) where extraction and filling takes place simultaneously. This kind of system is well-proven for
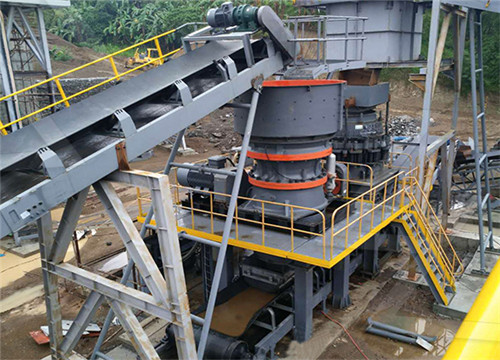
Open Access proceedings Journal of Physics: Conference series
of the mill is called raw meal and is accommodated in the blending silo. With the right composition, raw meal will be transported to the preheater for preheating and kiln is the main equipment of the
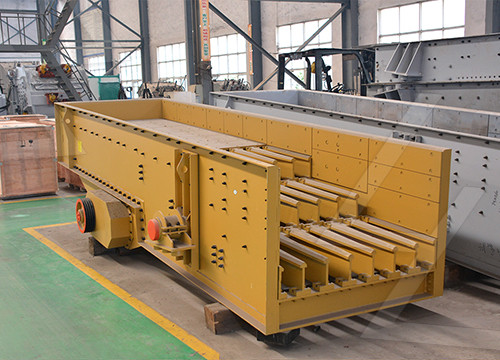
Plant Maintenance Modelling Through Availability Analysis In Raw Mill
2020年12月29日of the mill is called raw meal and is accommodated in the blending silo. With the right composition, raw meal will be transported to the preheater for preheating and kiln is the main equipment of the
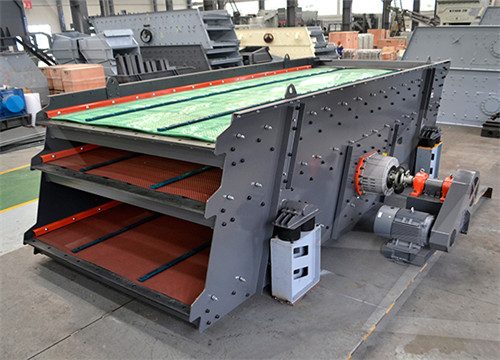
Preliminary Design of Eco-City by Using Industrial Symbiosis
the fine material will be continued to blending silo for homogenizing process and course material will come back again to the raw mill (compartment II). The homogenizing process in blending silo is really important to get appropriate material composition and reduce fluctuation in the quality of raw mix, because performance of kiln will be
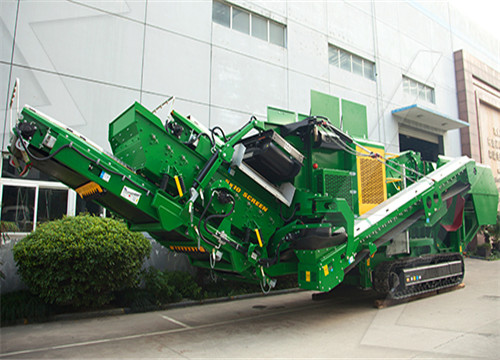
sbm/sbm raw mill blending silo.md at master sbm
You can not select more than 25 topics Topics must start with a letter or number, can include dashes ('-') and can be up to 35 characters long.
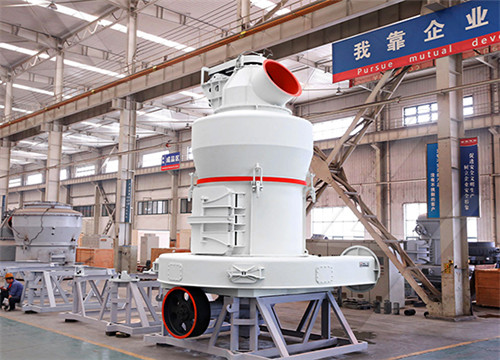
abstract fls raw mill razoriteolivedale.co.za
Abstract Fls Raw Mill Blending Silos Advanced Technology For Ne. SPIRAL SILO Brief Spiral folded silo technology is originated from Germany and SRON modify their technology about spiral steel silo While digesting the Germany advanced spiral silo technology and combing with the reality of our customers we have successively
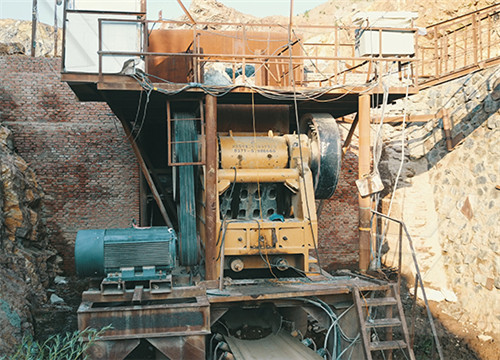
Alan Gee Lehigh Hanson/Heidelberg Cement Group Quality
2018年8月3日Alan Gee Lehigh Hanson/Heidelberg Cement Group Quality Control in the Cement Plant
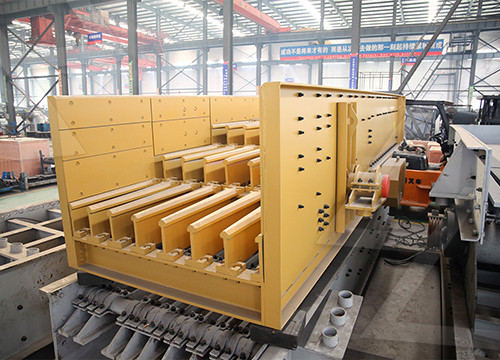
Emission reduction through process integration and exploration of
2023年1月7日The product, after grinding from the raw mill, is transported via air slides and bucket elevators to the homogenizing silo. Homogenizing silo is the prerequisite for raw mill blending to achieve kiln feed consistency. This also ensures regulated feed with minimum variation in quality for the smooth operation of the kiln. The raw mill is
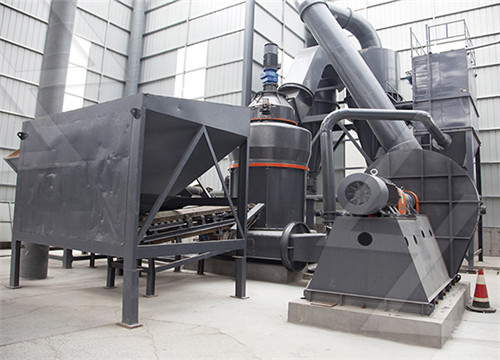
Blending systems and control technologies for cement raw
Diminishing the size and complexity of blending and stocking equipment before and after the raw mill represents a common strategy for reduction of capital and operating cost. The stone discusses the choice between X-ray fluorescence (XRF) and /spl gamma/-ray analysis sensors. Cross belt analysers used in the stockyard are also discussed.
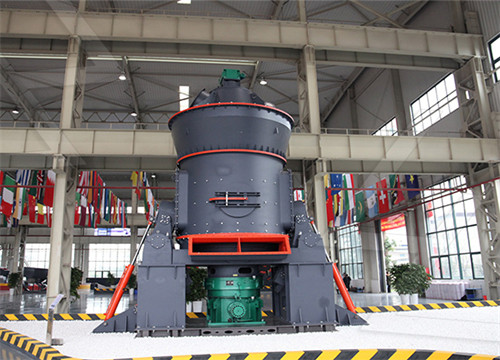
CFMI silo
raw meal blending and storage silo and with the CFS (Controlled Flow Storage) storage silo. The key word in the design of the CFMI silo is reliability. The challenge Ceiling of 4-compartment silo Bottom of 2-compartment silo. Project Centre Denmark A/S Vigerslev Allé 77 DK-2500 Valby Copenhagen Tel: +45 3618 1000 Fax: +45 3630 1820
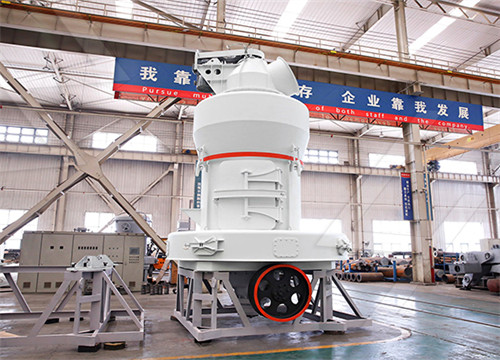
Plant Maintenance Modelling Through Availability Analysis In Raw Mill
2020年12月29日of the mill is called raw meal and is accommodated in the blending silo. With the right composition, raw meal will be transported to the preheater for preheating and kiln is the main equipment of the
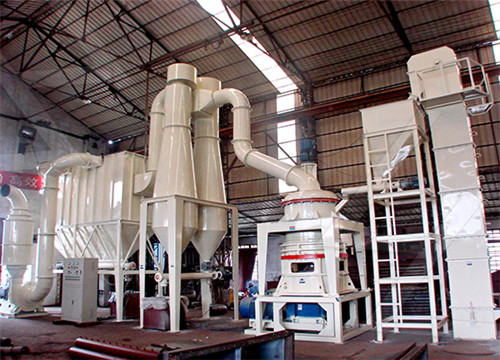
Fuzzy controller for cement raw material blending
2007年3月1日Abstract and Figures The main goal of raw material mill blending control in the cement industry is to maintain the chemical composition of the raw meal near the reference cement modules...
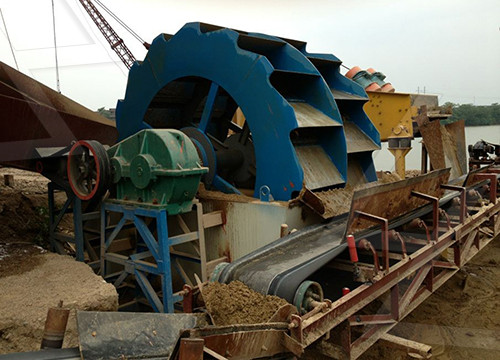
Azerbaijani cement production by Norm Sement Global Cement
2015年12月8日The raw meal is collected from the bag house filter hoppers and transported to a 550t/hr bucket elevator that feeds into an inverted cone-type blending silo with a design-blending ratio of 7:1. The 20,000t capacity blending silo can supply enough raw materials for 2.5 days of kiln operations. Under the blending silo there is a 180m 3
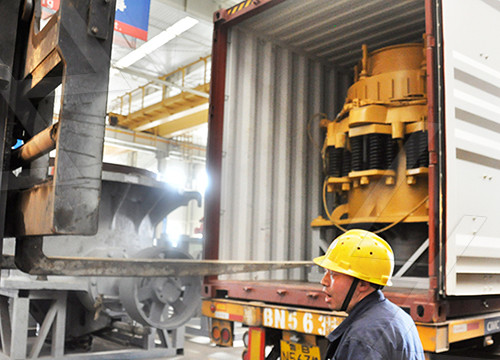
Silo Technology Zeppelin
The Multi-Flow blending silo is the ideal choice partic- ularly for retrofitting conventional silos with blending technology. System description The Zeppelin Multi-Flow blending hopper generates various flow velocities in the hopper and the lower cylinder area. This results in different dwelling times, which have an impact on the blending effect.
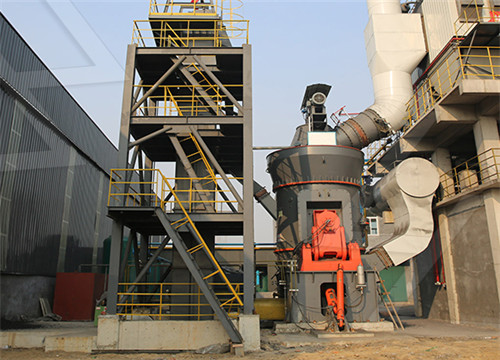
Raw Material for Cement Cement Blending |Amrit Cement
A raw mill with a superior fineness and well-controlled chemical composition using as advanced control system can improve the cement quality and define critical cement craft parameters. Amrit Cement uses the best of raw materials and has an enviable infrastructure supported by advanced technologies to ensure supreme cement quality.
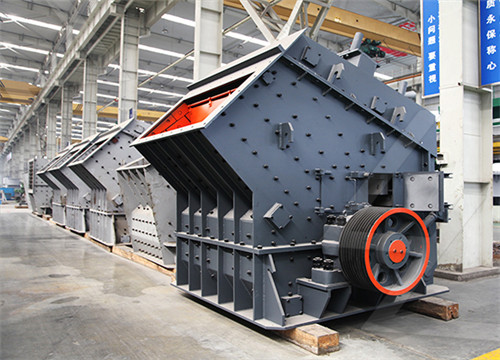
Description of Raw Meal Blending PDF Physical Sciences
Description of the CF-silo The CF-silo is a continuously operating blending and storage silo for raw meal. The operating principle of this silo is to extract raw meal at different flow rates from several outlets in the silo bottom and mix these streams together. The silo is laid out as a cylindrical building with a raised bottom as shown in
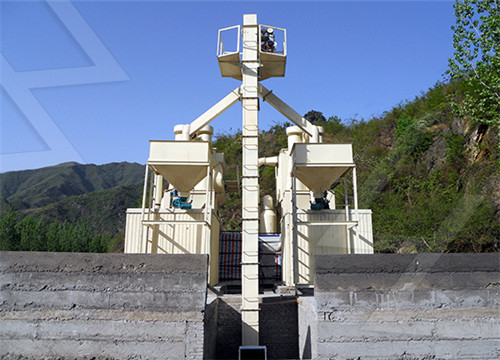
Birla Shakti
An electrostatic precipitator/bag house de-dusts the raw mill gases and collects the raw meal for a series of further stages of blending. The homogenized raw meal thus extracted is pumped to the top of a preheater by bucket elevator. In Pre-heaters the material is
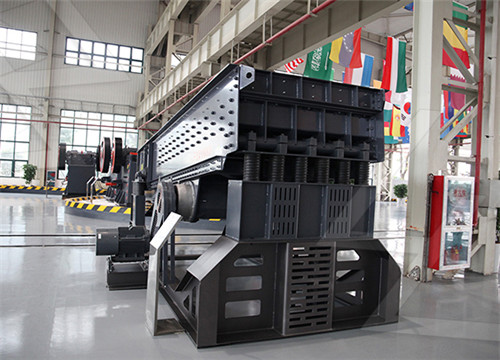
Intro Iteca Eng PDF Mill (Grinding) Cement Scribd
Blending Silos Raw Mill. Crusher. Clinker Silo Cooler. Kiln. Analyser FX3500 Chemical composition analysis 7/h Al Fe Ca Si P Cl Mg Cement Silo Cement Mill On line Process Control Raw Mix Sampling in a chute. Screw Sampler PREC100. Piston Sampler P11. Mechanical Transport. Sampling in an airslide Slot Sampler PF106. Mixing Hopper
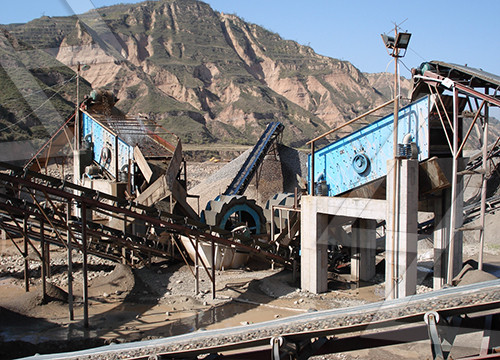
Preliminary Design of Eco-City by Using Industrial Symbiosis
the fine material will be continued to blending silo for homogenizing process and course material will come back again to the raw mill (compartment II). The homogenizing process in blending silo is really important to get appropriate material composition and reduce fluctuation in the quality of raw mix, because performance of kiln will be
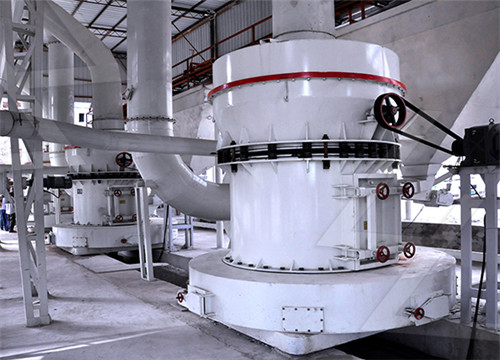
sbm/sbm raw mill blending silo.md at master sbm
You can not select more than 25 topics Topics must start with a letter or number, can include dashes ('-') and can be up to 35 characters long.
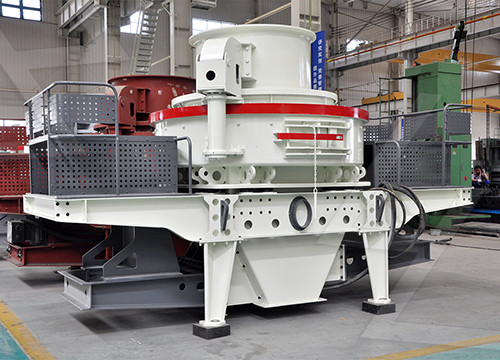
Keystone Cement CementLime MiningMetals CCC
CCCG managed and controlled the master schedule and all work activities as directed by Keystone Cement. . The plant was built to produce 3000 ST/PD. Services Involved. CCC was responsible for all Civil, Structural, Piping, Electricalinstrumentation and Mechanical in support of the installation of: Raw Mill.